In Upstate New York, the Catskill Region is known for its wild and abundant landscape, which artists, hikers, and travelers have long sought out as a perfect retreat. With undulating hills, dense forests, and rolling rivers, it’s a place that brings a sense of solace and peace. It was this environment that inspired The Catskill Project, an innovative, 90-acre community that sets Passive House design principles at its core.
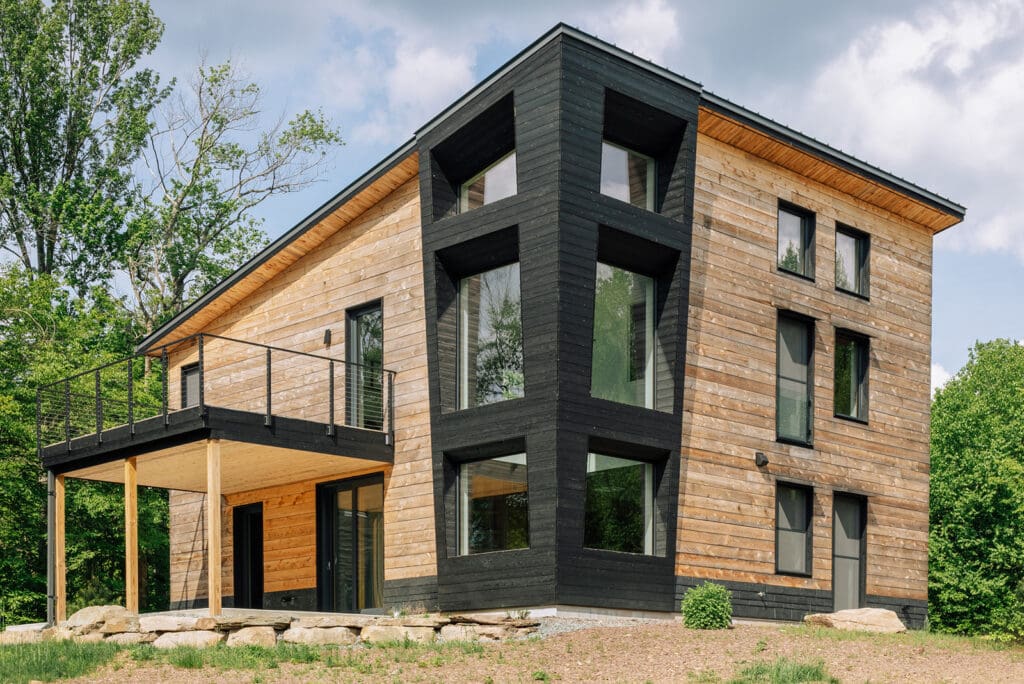
A Pioneering Approach
“It’s the respect of the environment and those underlying, embedded ecological systems, which are driving our design and thought processes,” described architect Buck Moorhead (BMA). An overall goal of the project is carbon neutrality, both in development of the site and in creation of each Certified Passive Home.”
Located at the gateway to the Catskills in Livingston Manor, NY, the property offers residents three to six-acre lots, which have been carefully cleared, taking down as few trees as possible. The hardwoods that have been harvested—cherry, ash, and soft maple—have been milled locally and made into flooring and ceilings for The Catskill Project homes.
The intention of each carbon-neutral house is to actively contribute to the health and well-being of those who live in it. And that’s how our part in the story began. When The Catskill Project team first reached out to us, they were interested in our prefabricated, energy-efficient Unity Homes.
But after hearing more about their aim to create multiple, high-performance structures at Passive House certification level, another possibility came to light. The project seemed like a perfect candidate for our Tektoniks Program which, in partnership, connects our high-performance building systems to others in the industry whose objectives are aligned with ours. By using this approach, The Catskill Project benefited from our prefabrication capabilities. The precision possible in our factory makes Passive House performance a replicable outcome instead of an exceptional achievement, including the stringent airtightness standard (0.6 ACH@ 50 Pa).
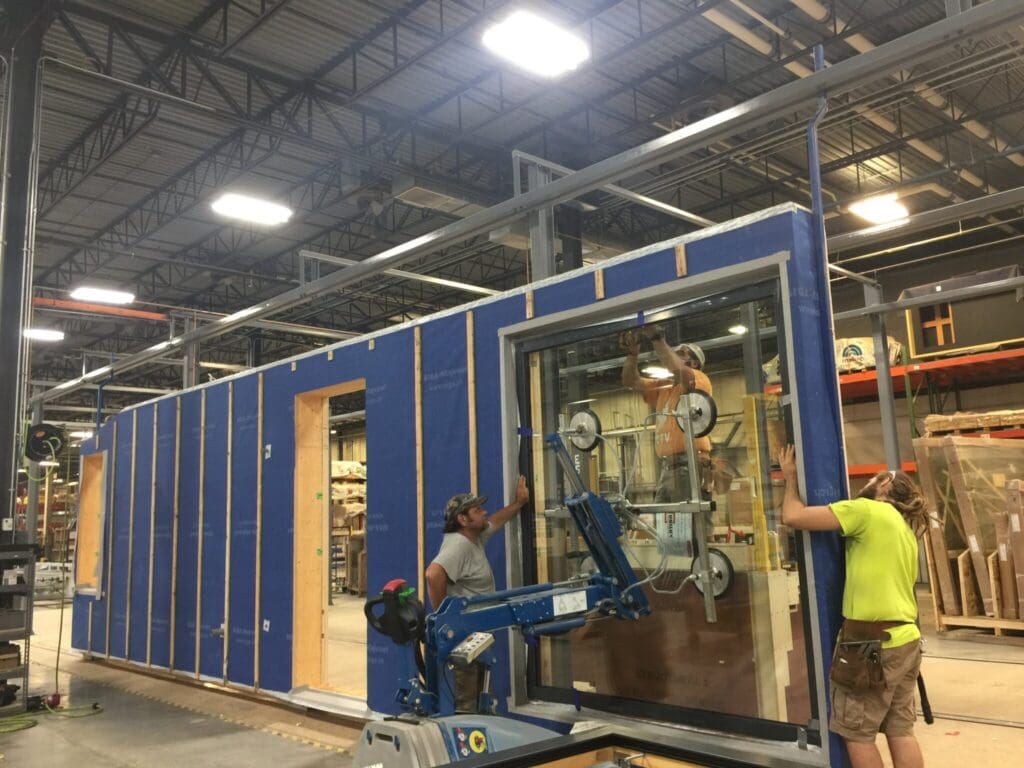
The Catskill Project benefitted from our factory-precision fabrication capabilities which makes the Passive House level requirements a replicable outcome instead of an exceptional achievement
Principles of a Passive House
As company founder Tedd Benson said, “Our collaboration with The Catskill Project has been incredibly well-aligned from the start because of their goal to reach homebuilding’s highest performance standard. The Catskill Project is committed to achieving the Passive House standards that are difficult to achieve in the field, but in our factory, it’s a natural outcome of our typical production process.”
In fact, all Bensonwood projects are guided by the five principles of Passive House Design.
- Continuous Insulation – thermal bridge free design helps to reduce a building’s heating and cooling needs, improving comfort.
- Airtight Construction – minimizing infiltration of outside air, and loss of conditioned air, is important for durability of the enclosure as well as energy savings.
- Optimized Windows – high-performance double or triple-paned windows and doors, depending on climate and building type, with additional focus on proper heat gain and orientation in the design.
- Balanced Ventilation – high-quality ventilation with heat recovery reduces energy loss and enhances air quality.
- Minimal Mechanical Systems – “right-sized” equipment that uses minimal energy to handle low heating and cooling loads.
Learn more about our approach to Passive House level design on our website.
The opportunity to apply these principles to an entire development versus one home at a time was an element of The Catskill Project that immediately impressed Benson. “Our company’s mission is to ‘…constantly advance our capabilities, capacity, and culture to bring the best standard of living to more people,’ so I was excited about the prospect that in one place that mission could be multiplied.” When Tedd went to New York to walk the land with the Catskill Project founders, the shared values and objectives became the basis for an on-going partnership.
Our Mission
To constantly advance our capabilities, capacity and culture to bring the best standard of living to more people
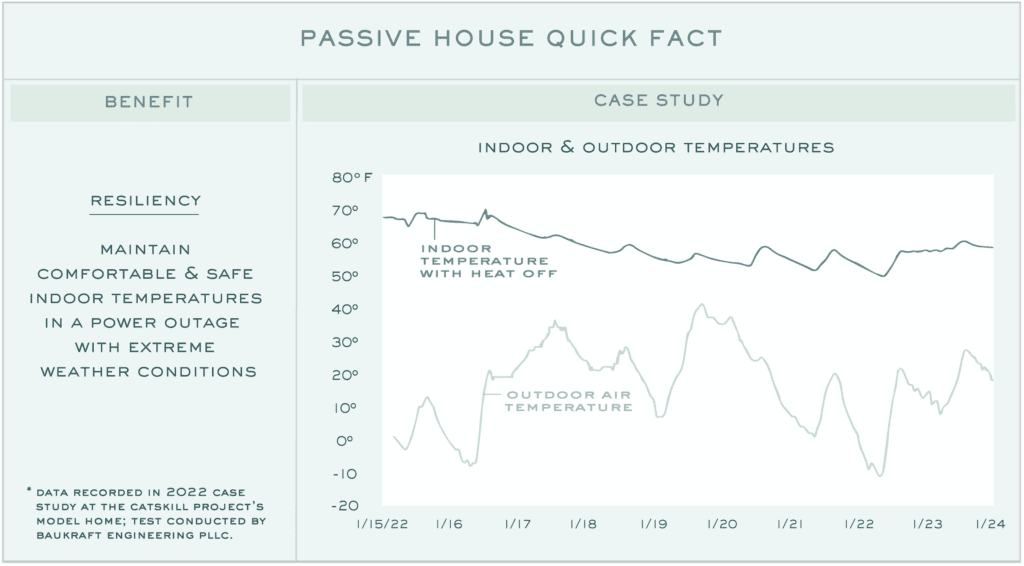
Panel Systems Designed to Perform
“We’ve been very fortunate to be partnering with Bensonwood,” Moorhead noted. The architect’s Passive Home plans were an excellent fit for the high-performance wall and roof panel systems fabricated by Tektoniks.
Above and beyond Passive House performance, our building enclosure system is ideal for The Catskill Project because it can be fully customized to suit any project’s specific needs. With the advantage of off-site prefabrication in our state-of-the-art manufacturing facility, we can guarantee a higher quality, more consistently built structure, with greater cost certainty and faster turnaround than traditional construction methods.
For the first home built in this development, Bensonwood’s crew assembled the entire building shell in just three days. The Balsam model home is now fully complete, furnished and ready for visitors to tour and learn about the community. Two additional Balsam model homes are now being completed after being raised in the fall of 2022.
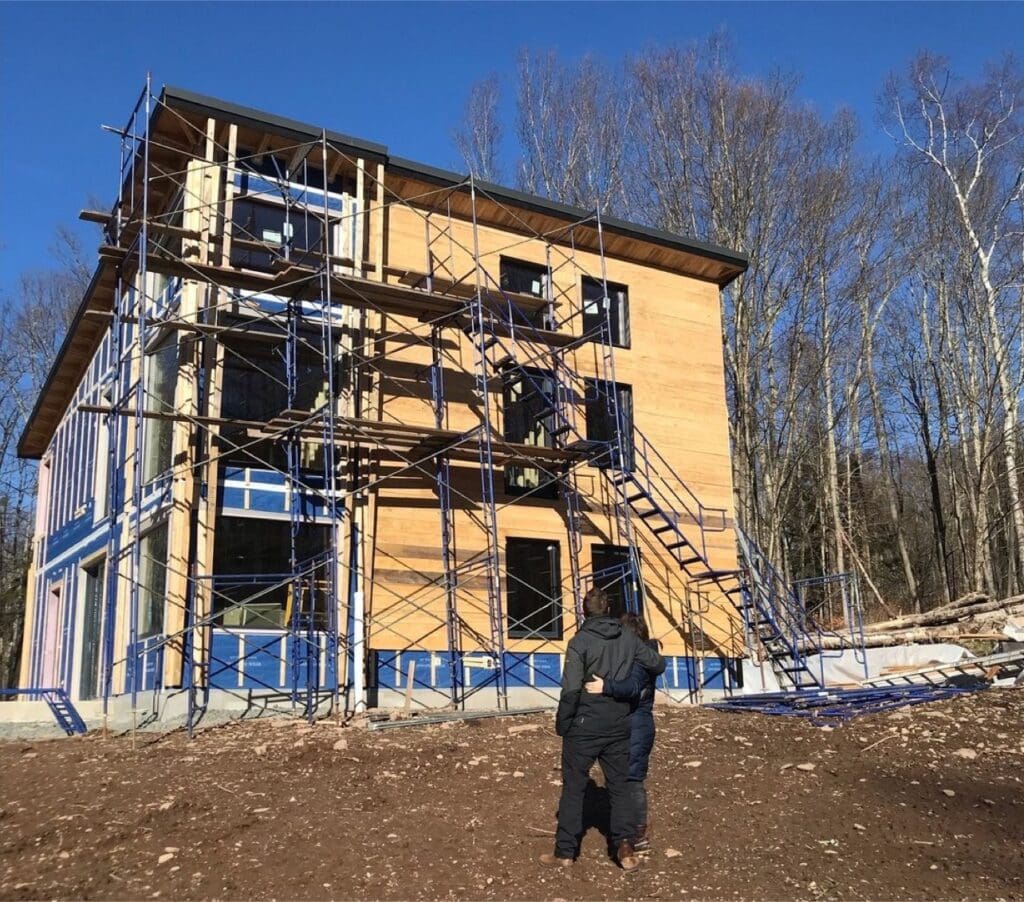
Making it Official
The Catskill Project is now in the process of receiving Passive House Certification based on the Balsam model. This includes a ‘Blower Door’ airtightness test to confirm the airtight construction.
To achieve the airtightness required for Passive House certification, there must be a maximum of 0.6 air changes per hour at 50 Pascals pressure. In addition, the home must require very little energy to maintain a comfortable temperature year-round. When tested internally, the Balsam model home met each of the criteria and demonstrated exceptional performance.
Bringing It All Together
When our part was completed, an impressive team of local carpenters, plumbers, electricians, painters, and other tradespeople descended on the site to make the Balsam as beautiful on the interior as it is on the exterior.
From inside, expanses of nature can be viewed from every angle, particularly through the soaring great room’s oversized windows and from the contemporary kitchen with its floating shelves. Details like porcelain tiles, Kohler fixtures, and highly durable FSC® certified Richlite Black Diamond countertops bring the entire space together.
Perhaps most notably, the home will remain at a comfortable temperature in any season and those living inside will benefit from continuous, filtered fresh air. This is due to meticulousness of each step in the fabrication process, from the precision robotics utilized to construct the high performance shell to the rigorous inspection and testing of every component that comes off the line.
Additional features of these homes include:
- Frost-protected, slab foundation
- WFB10 wall with continuous insulation and insulated service chase (R-47)
- Roof with 16” cellulose with insulated service cavity (R-60)
- Unilux tri-pane wood-aluminum windows (U-0.15)
See more details and photos of this project on our portfolio.
An individual who stayed at the model Balsam home for a test experience before purchasing a house within the development, described, “we quickly realized the benefits of passive house design during our stay at the model house this winter. With the temperature set at 68 degrees, we were prepared to turn the heat up to at least 70 degrees upon our arrival, but it wasn’t necessary as we had a very cozy and comfortable indoor temperature all weekend long. The efficient windows and superior insulation (and the elimination of air leakage) kept the additional layers we packed in preparation for a cold winter weekend packed in our travel bags until we returned home.”
With minimal operating and maintenance costs, these homes, built with resiliency in mind, illustrate the possibilities and highlight the benefits of carbon-neutral living, passive house design, and panelized construction. Moorhead noted: “We consider this project to be a new paradigm for the future of living in a rural environment.” It’s a project we’re certainly proud to be a part of and one that has allowed us to bring a better way to build to more people.
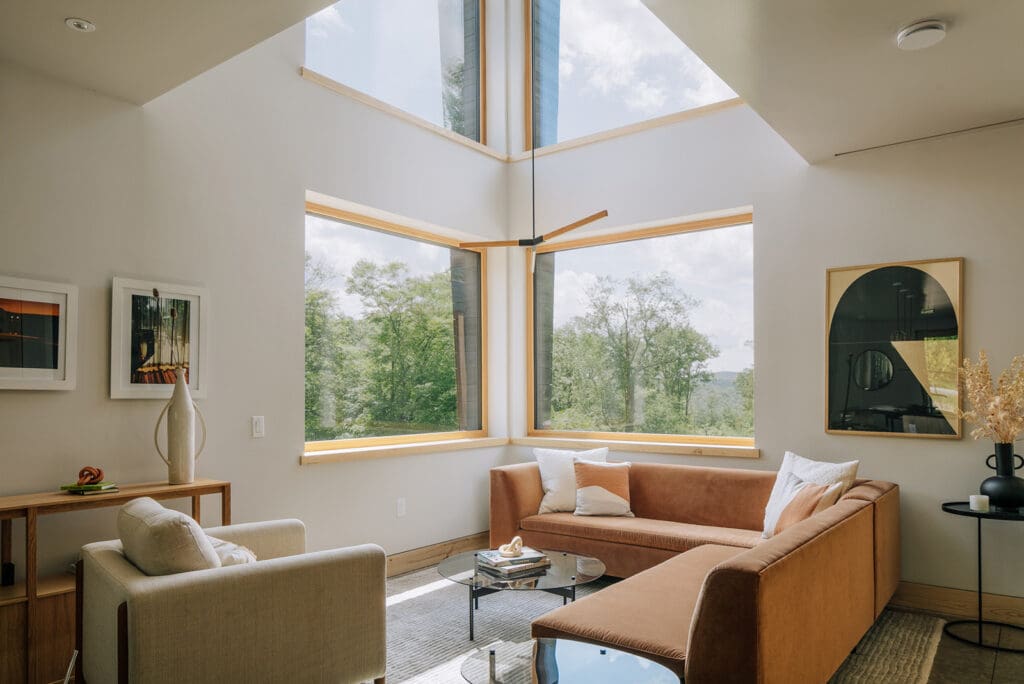
To learn more about the first carbon neutral community in the Catskills, visit their news page here.
We consider this project to be a new paradigm for the future of living in a rural environment.
Buck Moorhead